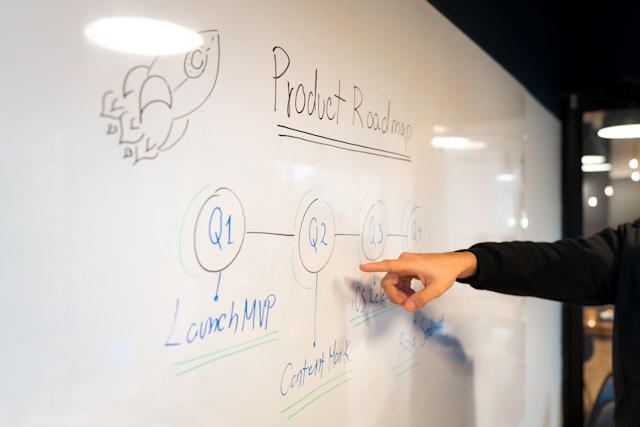
What Will You Learn?
- Define the key concepts of Lean Six Sigma
- Recognize the importance of data-driven decision-making in process improvement initiatives
- Apply essential Lean Six Sigma tools and techniques to real-world problems in a workplace setting
- Analyze simple process-related issues using Lean Six Sigma methodologies to find practical solutions
- Explain the roles and responsibilities of different Lean Six Sigma belt levels in an organizational context
- Identify various types of waste in processes and understand how to eliminate them to improve efficiency
- Describe the fundamental concepts of Lean Six Sigma, including its principles, methodologies, and tools
- Illustrate how Lean Six Sigma principles can be integrated into daily work processes to foster a continuous improvement culture
Course Curriculum
Lean Six Sigma White Belt: Introduction
Understanding Quality
Understanding Six Sigma
The Seven Basic Tools of Quality
Understanding Lean
Student Ratings & Reviews
No Review Yet
No Data Available in this Section